 |
|
Woodworking Projects - 2013
|
|
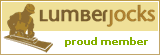 |
|
Wednesday, January 9, 2013: My granddaughter, Chloe, is a fan of Thomas the train engine. I came up with the idea of making her a replica of Thomas which can be hung on her wall. It has a couple of places to hang clothes and a secret hiding place for special items girls like to keep. Be sure to click on each photo, there are more assembly photos behind each photo here. |
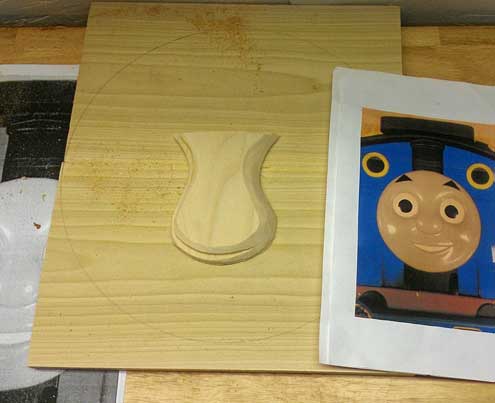 |
This turned out to be a bigger project than I first imagined. I had to wait for some special tools to arrive to complete some of my ideas. While shopping, I took photographs of Thomas and also visited the Thomas Website to get copies of Thomas face. From planning to completion was about 2 months. The face is made of Poplar. I used my scroll saw to cut out the rectangle which will hold the secret cabinet. |
|
|
I used the Foredom Flex Shaft Power Tool to do some shaping. The round face had to be made from two Poplar boards glued together. I purchased the largest plastic eyes I could find for the Thomas "look". The make the curve in the roof, I glued two pieces together bending to the shape of the roof. Once the glue dried, the roof had a permanent curve. |
|
I struggle with painting. I have no painting talent and don't particularly like doing it, especially if detail is required. I purchased a selection of acrylic paint to get all the colors I thought I might need. In the left photo, I'm painting the small wooden boxes I purchased at Michael's. I chose four primary colors and alternated the colors on the drawer pulls to match the drawer colors. All the pieces are starting to come together. I want Chloe to have strong pegs to hang her coat and other things so the front bumper it beefy. I painted Thomas face gray because that seemed to be the color in most illustrations I found. |
|
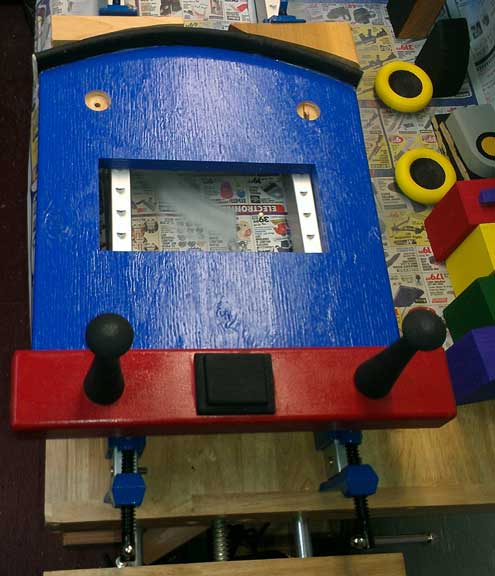 |
After painting, the pieces are glued together then clamped. The holes drilled in the top of the cab are for the yellow framed port windows. This is how the cabinet will be secured to the wall. The port windows have a tenon on the back to fit the hole. My intention is to mount to the wall, then put a drop or two of glue onto each tenon then push into the screw hole to cover the screws. Only a drop or two of glue so the ports can be removed if Thomas needs to be moved sometime later. |
|
|
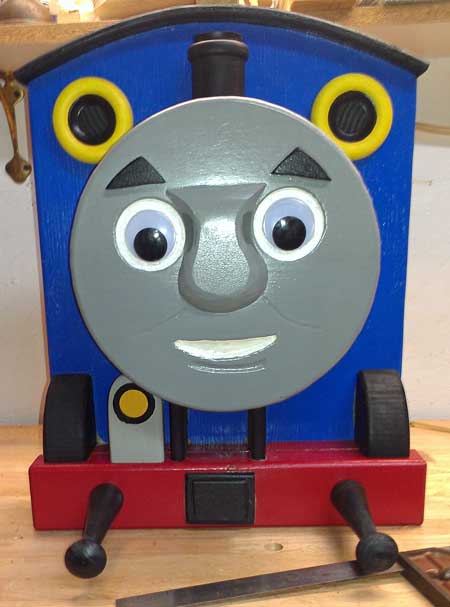
The pieces are glued to the body. Thomas face is attached to the tiny cabinet using a piano hinge for strength. The cabinet is secured to the body using counter-sunk screws. It was a tight fit inside the cabinet turning the screws. I did buy a used lathe figuring my make-shift drill press lathe was going to kill me. The Thomas smoke stack was my first turning on my new lathe. I turned it from scrap Birch found at a second hand store for $1. It looked so good, I hated to paint it but Thomas must have a black stack. When mounted to the wall, Thomas face opens by pushing his left eye brow to reveal four hidden drawer when Chloe can put her treasures. The latch is a spring loaded magnetic latch similar to the latches used on glass front sound system cabinets. When the latch is pushed, the door pops open. To close, just push the eyebrow again. Now I can work on other projects with Thomas off my workbench. I hope this is a big deal to Chloe. |
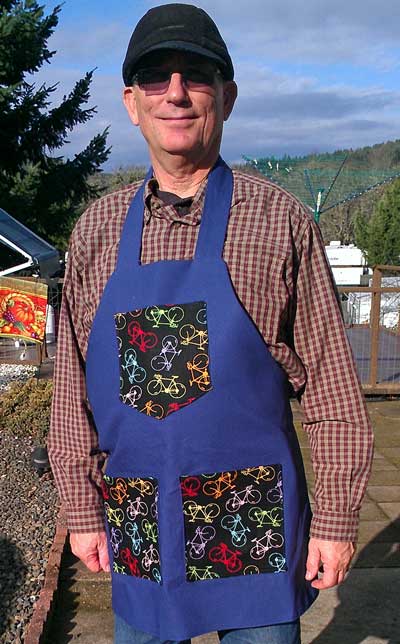
Friday, January 11, 2013: I'm modeling my new shop apron Gwen made for me. Yes, it is cold but look at that blue sky behind me. It's made of denim (Gwen says she'll never work with denim again) with a liner. The liner has road bikes as the design, my other passion. I can't believe how handy it is. I usually come out of the shop covered with sawdust, the apron helps to keep that off my clothes. But the pockets are what really make it great. I keep a pencil and ruler in the top pocket plus 4" square and my cell phone in the bottom two pockets. I'm sure I'll put other items there soon, just have to figure out what I go after the most. Click the photo to see the liner better.
First thing I did today was head to Costco for an optometrist exam. It's been more than a year and I'm ready for some new glasses. With my eyes dilated, I was pretty much "blind" for the rest of the day but I still managed to find some items at the dollar store and Michael's I wanted.
By 4:00pm I had recovered enough to continue working on a tool rest for my bench grinder. I need to turn some wood parts for the locomotive I want to build for the grandchild but I need to sharpen my chisels first. I believe I can have that project finished in a couple of hours after visiting the hardware store for some nuts and bolts. |
|
|
|
Sunday, January 13, 2013: OK, so hundreds of woodworkers emailed me asking me to illustrate the tool rest I mentioned Friday. This was not an original idea, the idea came from Woodturning, a Foundation Course by Keith Rowley. I followed his pattern almost exactly with the exception of the height of the legs. Keith wants you to buy the best grinder you can afford. I did just the opposite, I bought the cheapest grinder, one which was on sale before Christmas at Home Depot before Christmas for less than $25. My grinder has 6" wheels while his grinder has 8" wheels, so my legs are and inch shorter. Other than that, I followed the pattern exactly. Here is a PDF copy of the pattern. I've sharpen all but one chisel using this tool rest and I'm very impressed with how easy the rest works. There is one problem however. When you view the left photo, note how close the handle is to the rest. I can imagine, with multiple sharpenings, the blade will become shorter and the handle will eventually hit the rest. Indeed, I was unable to sharpen my skew chisel for this reason, the handle kept the blade from touching the wheel. Of course, these are CHEAP chisels. I paid $18 for 8 chisels at Harbor Freight. That's $2.25 per chisel. Compare my roughing out gouge in the photo above to this roughing out gouge
for a mere $95.81 (free shipping). That's $95.81 for ONE chisel. Of course, it will likely hold an edge much longer than my $2.25 chisel. I'm not new to woodturning. I owned a lathe 30 years ago and did a few turnings but NEVER sharpened my chisels (so I must have really done a FEW turnings). Now I'm much more serious in wanting to turn some toy parts and other items. So I must learn how to sharpen a chisel. I'd MUCH rather learn sharpening skills on my $2.25 chisels than on a $95 chisel, get my meaning? Click the right photo to see how good a job I did when sharpening my gouge. I believe I will modify the tool rest platform a bit to fit shorter blade chisels. If that doesn't work, I make a new, shorter platform. Apparently Keith's chisels are longer. I've already had to re-sharpen my gouge three times (once for each project) so I'm getting good practice. I know real woodturners are rolling on the floor laughing at my $2.25 chisels but I lose nothing if I screw up when sharpening one of these. |
|
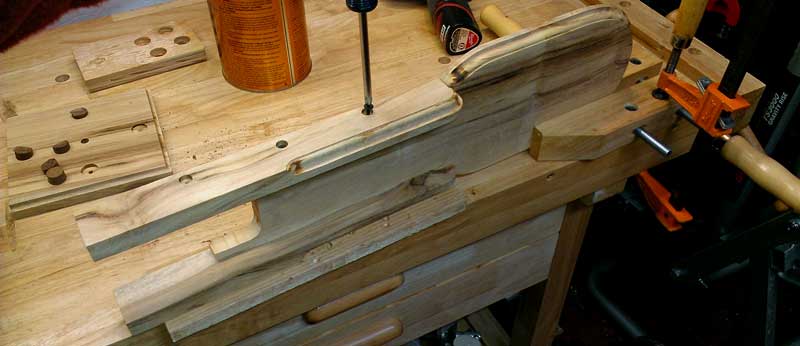 |
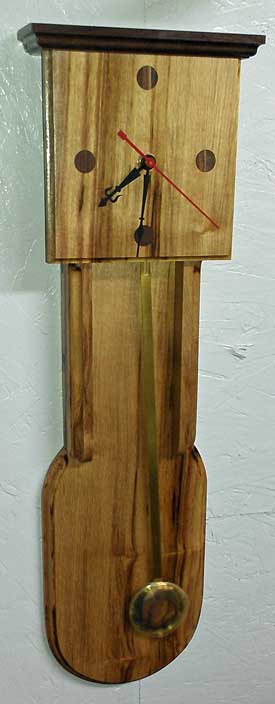
Monday, January 14, 2013: I've finished the Myrtlewood clock I have built for my daughter and her new husband. I will be visiting them in about ten days and I wanted something special for them. I already had the clock movement on hand and had purchased the Oregon Myrtlewood some weeks ago so that gave me the idea for the clock. I love pendulum clocks and hope Mindy and Scott do too. This movement does NOT chime but does make a subtle "clunk" once every second. I thought it was a silent movement so was surprised when I heard the "clunk". Oregon Walnut makes a nice contrasting wood to accent the Oregon Myrtlewood. I used Oregon Walnut on top of the clock, as time reference points on the front and three accent points on each side of the clock. I used a plug cutter to drill the plugs in the Walnut then a "bent handle" chisel to slice the plugs smooth. I DID use a couple of the plugs to hide screw heads but just as many plugs as artistic points. The clock measures 2 feet tall and 7 inches at the widest point. Click each of the photos for additional assembly views. |
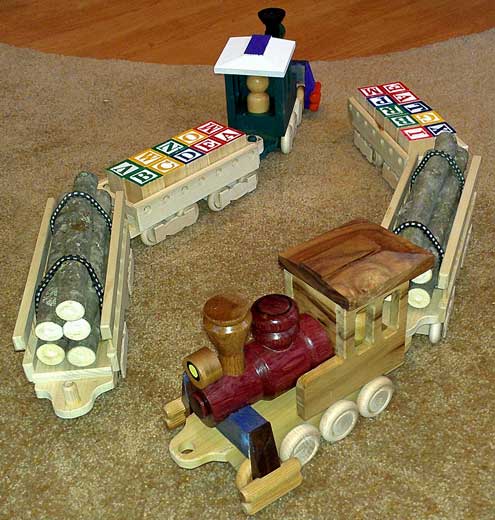
Thursday, January 17, 2013: This has been a serious project taking weeks to complete. I began with the train cars so I would know how tall to make the locomotives to match the train cars. I'm building two trains, one for my 16 month old grandson and one for my 3-1/2 year old grandnephew. Both trains are limited to two cars for this trip but I plan to add cars as the kids get older. Actually I plan to build at least one more locomotive, more for the long haul than this little "yard engine". Most of the wood in these trains is Poplar. No screws or nails, just glue holding the parts together. I roughly followed a locomotive design in the book, Great Book of Wooden Toys by Norm Marshall and Bill Jones. The cars were my own design but I plan to build some that are represented in the book with modifications. The book shows building the train using cup hooks to couple the cars which I refuse to do. Metal parts such as cup hooks are an invitation to injuries. They also detract from the heirloom quality of the project. The engineer is also my idea. This project began with the block cars. Click each photo to see additional construction and assembly views. |
|
The cars began with the wheel "trucks" under the cars. Two half inch wood blocks glued together make of the trucks. Each care requires eight wheels using these trucks. This design came straight from the book and turned out to be much more work than it looks. 1-1/4" wheels are used with the trucks but I didn't like the "tire look" of the wheels I had on hand so used a hole saw to give the wheels a better look for train cars. I built the jig for my drill press to hold the wheels while the hole saw cuts into them. |
|
I used my "zero clearance" insert on my table saw when making the rails for the block car. When walking into Lowes I spotted 1/4" pine yard sticks which I thought would add interest to the block car. I ran a dado down the center of the base before cutting out the shape so the yard stick become a part of the base. I also built a jig to trace the shape of the coupling ends using a screw point to give a center hole for drilling. |
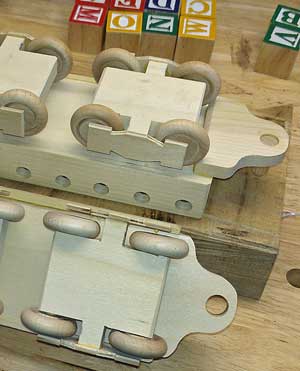 |
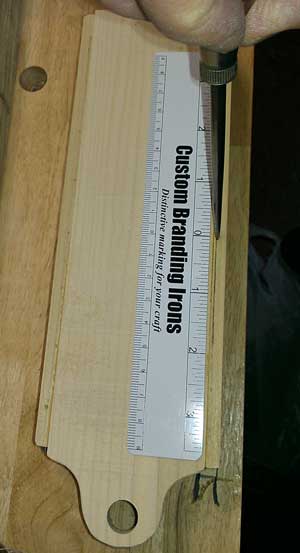 |
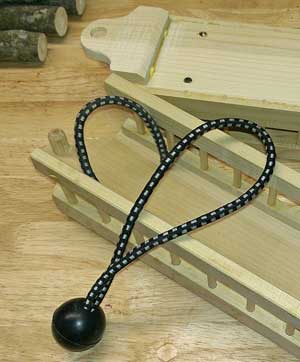 |
Trucks are glued to the base of the block cars. The timber cars are about three inches longer than the block cars. I tried using 3/16" dowels for the side posts but 1/8" dowels were easier to install so one car got 3/16" while the other got 1/8". I felt a permanent strap was needed to secure the "logs" (fig branches) so cut the ball off a ball tie to glue the bungee cord to the car base. Five logs fit perfectly and tightly inside the strap. These cars got the same trucks. |
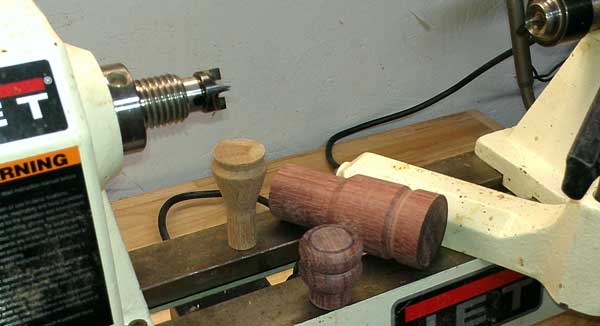 |
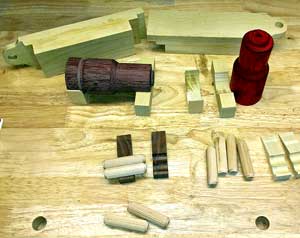 |
I used my new (used) lathe to turn the locomotive boiler and parts. The red boiler is turned of fig which I cut from my own fig tree several months ago. I used red food coloring because I wanted the boiler to look stained rather than painted. The other boiler is turned from Purple heart which I got by accident from the widow of a wood turner. She was liquidating all his wood and thought some pallets were built of Purpleheart. I purchased four pieces but only one of the four was Purple heart, the rest was Oak. I'm still happy with the purchase. |
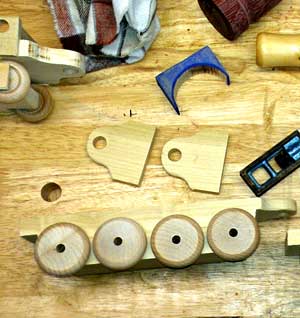 |
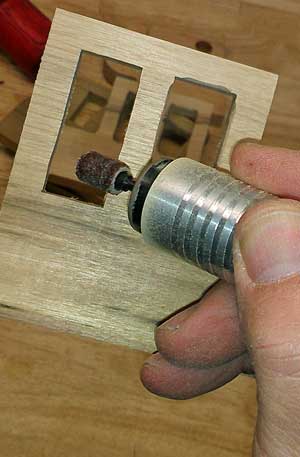 |
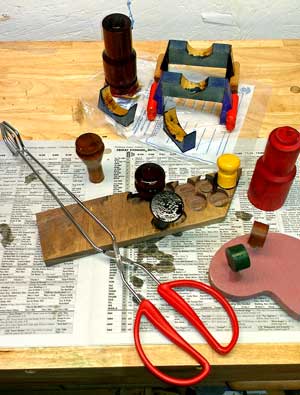 |
I used 1-1/2" rather than the 1-3/8" wheels in the book. The authors made their wheels by using a hole saw to create them. I don't like that idea so used purchased wheels which are turned on automatic lathes. I use to sell millions of these when I was in the blue print business for twenty years. The Foredom Power tool helped to shape the windows in the locomotive cab. I dipped many of the parts into polyurethane using togs I bought at the dollar store. |
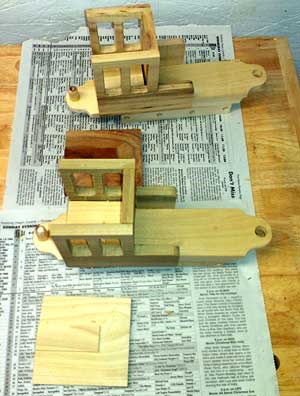 |
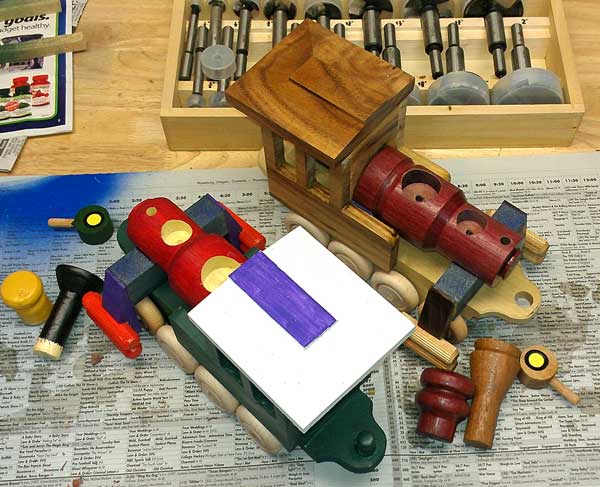 |
Final assembly took more than a day because I had to wait for glue to dry before proceeding to the next step. I chose to stain/paint one of the locomotives to add interest. The other locomotive has Oregon Myrtlewood for sides and some sort of imported hardwood for the roof. The roof wood was given to me by my friend John Hehn who lives in rural Sutherlin. It was a small piece of hardwood flooring which John figured I would find a use. The engineers inside the locomotives are removable but large enough that Noah (less than three years old) can play with it. My plan is to add a car to the trains every few months which will keep it special to these two boys. I also plan to build several locomotives to match the cars. I don't want to leave out Chloe, my grand daughter so I plan to built Emily for her to fit these cars. She likes Thomas and probably knows who Emily is. I like Emily because of the unique engine style. I think it will be fun to build and know she will be the only one with a model of Emily. |

Friday, January 18, 2013: A couple of weeks ago I received my custom branding iron so I can brand the items I make and give away. Since I have no space to keep anything, EVERYTHING I make must be given away. Hopefully branding the items will help the receiver keep them (or give them away) as heirlooms. After all, 50 years from now, who's going to know who "Dale Prohaska Jr" was? Interestingly, I dropped this train car while branding it and the end wheel cap and one of the wheel broke and the parts flew across the shop. So 50 years from now, this train car may not exist. Poplar may NOT have been a good choice for this train but local supply included Pine, Fir, Oak and Poplar. Perhaps I'll use Oak for the next cars. So everything is branded. Click the photo to see the crude stand I made to hold the brand to the torch.
Costco called today to say that my new glasses had arrived. I had an eye exam a week ago then gave them my old frame to install the new lenses. I also ordered a replacement for my "computer" glasses which have never worked quite right. In the mean time, I was using an old pair of glasses which worked fine until I dropped them outside the truck and ran over them. Now I was hoping for my "everyday" glasses to arrive but only the "computer glasses arrived. Darn! Maybe tomorrow.
I picked up items at Michaels and the dollar store to finish my current projects and visited Lowes for lumber to complete the next project. My daughter wants a "rustic" frame so I purchased rough cedar. We'll see how that turns out. |
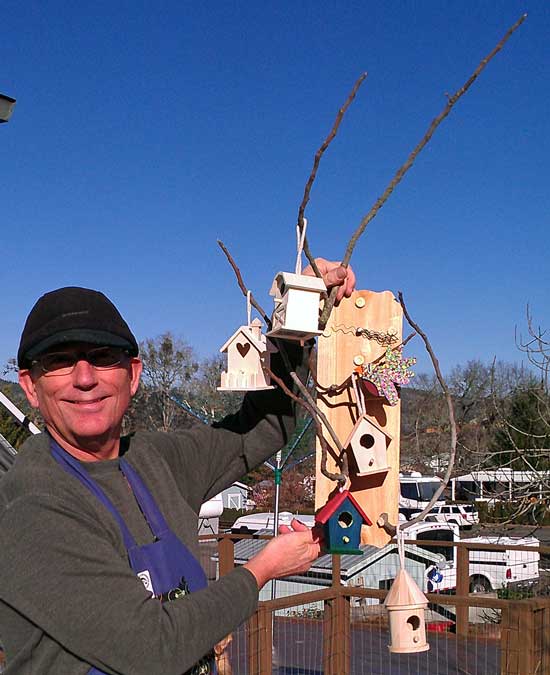
Monday, January 21, 2013: The final gift is what I call, the birdhouse clock. The clock is made of rough cedar and the left over fig branches I pruned a couple of months ago. The branches are glued to the cedar to hold them in place with the exception of the top branch which I'm holding in place. I don't want to glue it in place because it would likely break during transportation. The idea of the clock is for each member of my son's family to paint their own birdhouse and hang on a branch. So four of the five birdhouses are unfinished. |
|
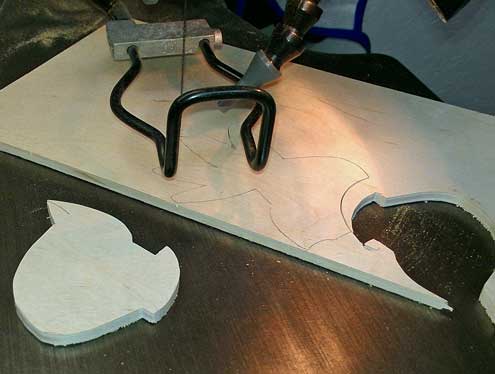
The clock was easy to make. Fortunately I have been storing the branches in my heated shop for a couple of months. They shrink as they dry so they must be dry to know what size hole to drill in the cedar to glue the branch. I didn't however, dry the branch pieces used for the four points of the clock face. I sized them using a plug cutter to 3/4" then remembered they were still "green". I put them into a microwave to dry them quickly. That worked great but they shrank to 5/8" so I had to create a new clock face since I'd already drilled the 3/4" holes. The bird I cut with the scroll saw, glued together, then painted and glued to a fig branch to mount to the cedar. Now I just have to convince my son and daughter-in-law what a great gift this is so they will hang it someplace other than the garage. |
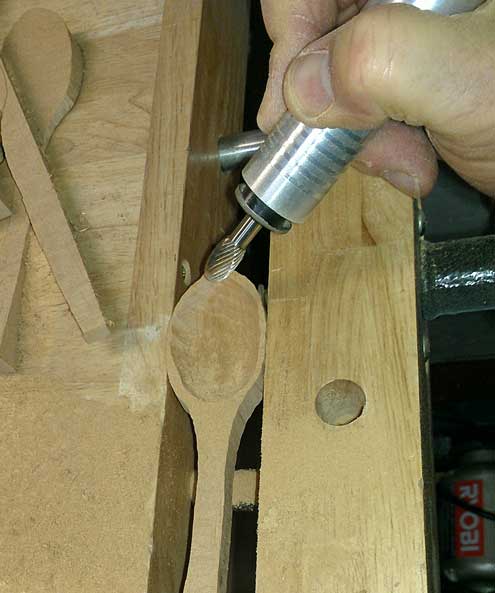
Tuesday, January 22, 2013: Gwen has made a very cute apron for Chloe, my 3 year old granddaughter. She wanted a wooden spoon for the pocket in the apron. I made a spoon and fork from some scrap birch hardwood I had in the shop. After sanding on the power sander, they came out pretty well and Gwen was pleased, I hope Chloe is too. Click the photo for another view.
This day was used completing items on my "to-do" list before leaving Oregon tomorrow. I'll first be installing a garbage disposer for my mother then transporting Mom and gifts to Reno for a visit with the grandkids (great-grandkids for my mom). |
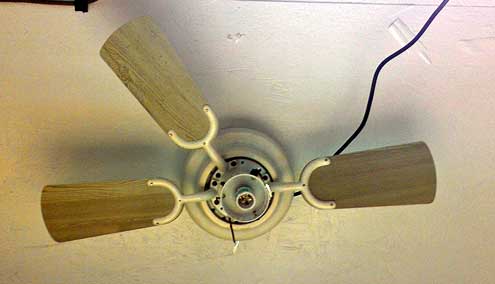
Wednesday, January 30, 2013: The priority today was to get all college course assignments scored and new emails sent out to students. I finished that by mid-afternoon which left me with enough time to install a ceiling fan in my tiny workshop. Here's the story behind the fan. First, it must be a 30" fan, nothing larger would fit. It had to be cheap, I didn't want to spend much on it but really wanted one in the shop. I subscribe to the online Orchard Supply Hardware (OSH)email alerts to sales and special promotions but there are no OSHs in Oregon. But, last week, I drove into California and then Nevada so I prepared by printing the most current promotion, a 15% discount coupon. It doesn't sound like much but OSH doesn't do much, in fact, they often have a "no sales tax" weekend which saves 8% for those poor California buyers. So I already new my 15% discount was really a savings of only 7% due to the sales tax. Well, while shopping in the Lodi, OSH for plumbing supplies for my mother's I spotted this fan "on clearance sale" with the display model the only model left. It was less than half price at $22.00. I asked the manager if I could use my 15% discount coupon on it. He replied, "sure". That made the sale. I paid about $20.00 for the fan including sales tax, the right price for my shop. The fan had everything I was looking for and more. It had three speeds forward and reverse operated by chain pulls and a simple switch to change direction of rotation, plus a light, which wasn't on my list of needs. I already had the wire to connect the fan so installation was easy. Click the photo for another view. I don't have a bulb yet, but when I do, the fan will also be a light. |
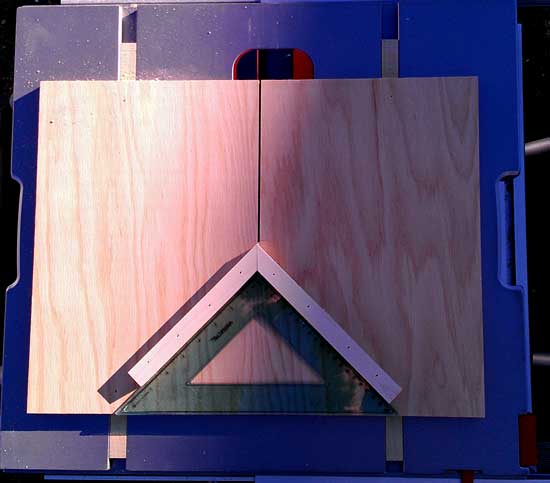
Saturday, February 2, 2013: I need to make some miter joints so today I built a miter jig for the table saw. I have two guides glued to the bottom of the base board which fit into the miter head tracks in the tablesaw top. I used a triangle to set the guides to the top of the jig base, then glue. Brads are used to hold the guide boards in place while the glue dries. I may add toggle clamps to hold down the boards for cutting but I haven't decided that yet. |
|
|
|
Tuesday, February 5, 2013: Last evening I got my second chance to visit the Roseburg Woodturner's club. They meet the first Monday of every month for demonstrations, show off of member's work and a raffle. Larry was the demonstrator at this meeting. He showed how to turn a travel mug cover for a steel travel mug insert. This mug cover was turned from cedar. Larry says he can turn one in 20 minutes and has done hundreds of them. Click the photos for additional views. On the member's table is a tall turning. This is all on piece, not pieced together. He had to have several intermediate supports to be able to turn something this long. |
|
|
|
| | |